Last Thursday our team was in Innsbruck!
Why? Given its intrinsic features, WeStatiX is the perfect software to build the digital twin of the new “Terfener Innbrücke” bridge.
The project
The Terfener Innbrücke (B74) at km 54.3 of the A12 Inntal motorway serves to overpass the motorway over the Inn, with a separate supporting structure for each directional carriageway.
The new construction of the Terfener Innbrücke is a 3-span prestressed concrete structure with a box girder cross section with one bridge support structure per directional carriageway. The supporting structures are erected in free cantilever from the bridge piers, without any downward support.
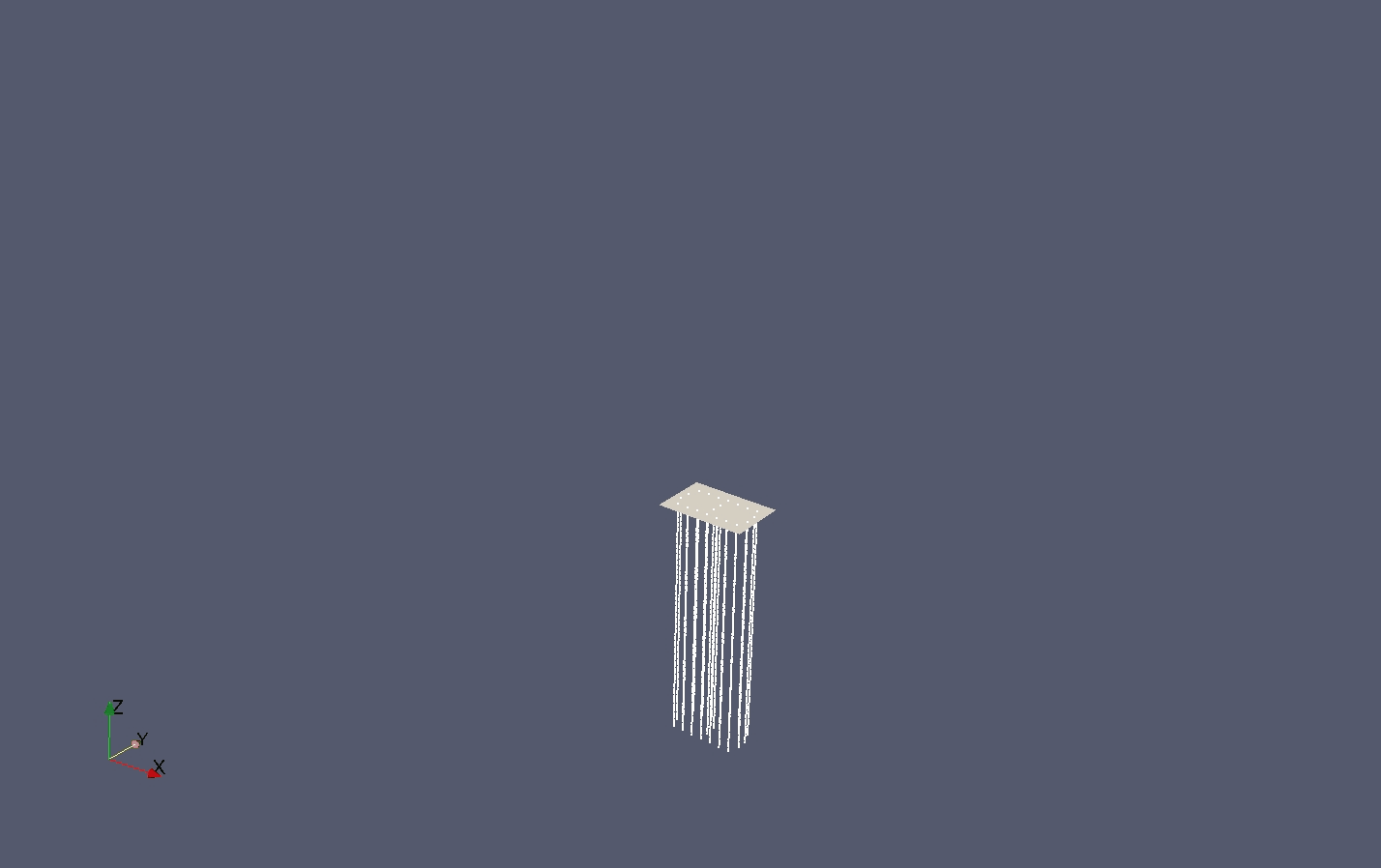
In order to increase the safety level for this structure, ASFINAG wanted an innovative and reliable monitoring system to be implemented, based on a digital twin.
What is a digital twin?
A digital twin is a living model that drives a business outcome (Colin J. Parris).
It’s not just a sketch and it’s much more than just a 3D model: it is a powerful tool to communicate with a structure and to keep it monitored, all in real-time!
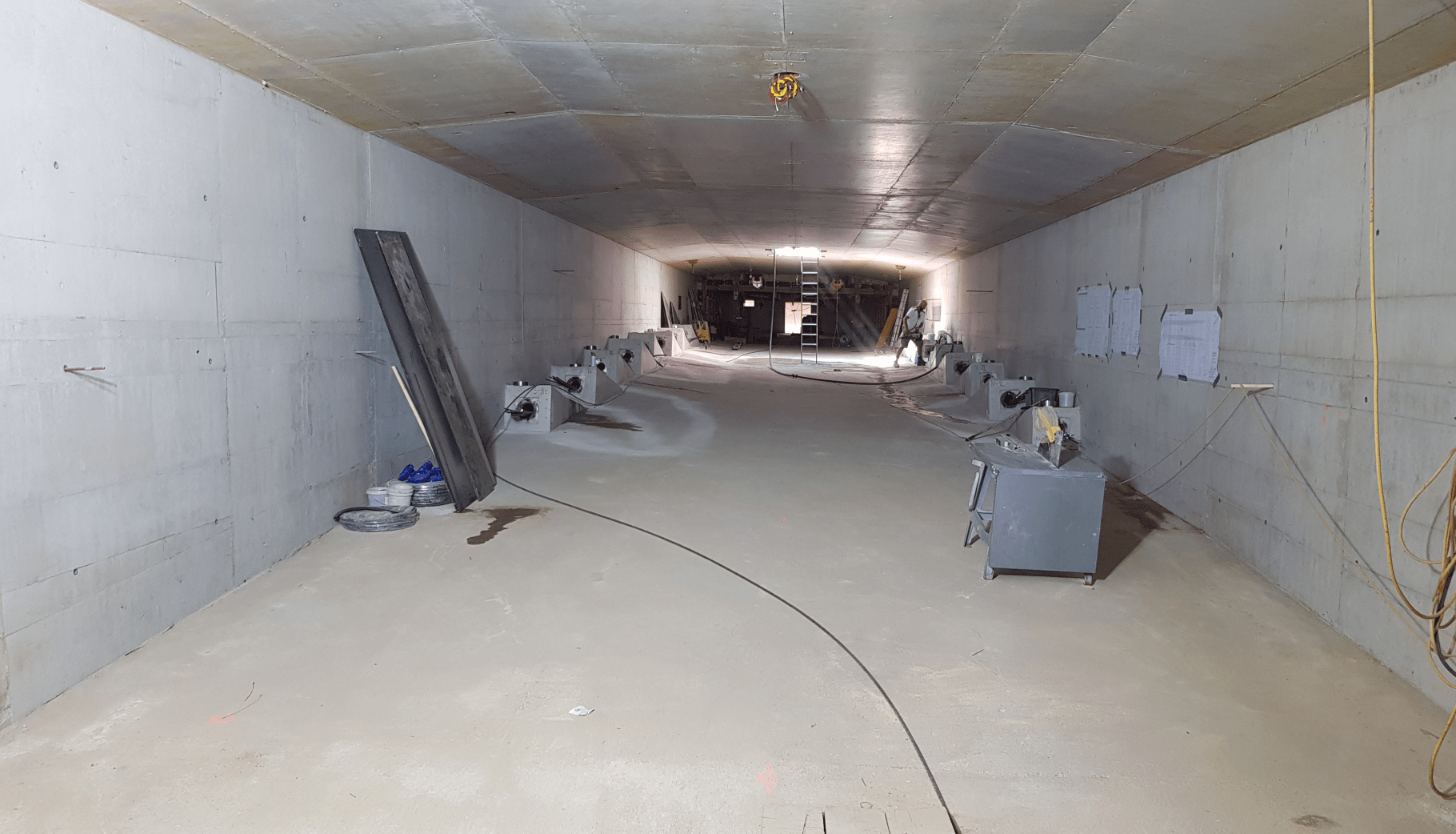
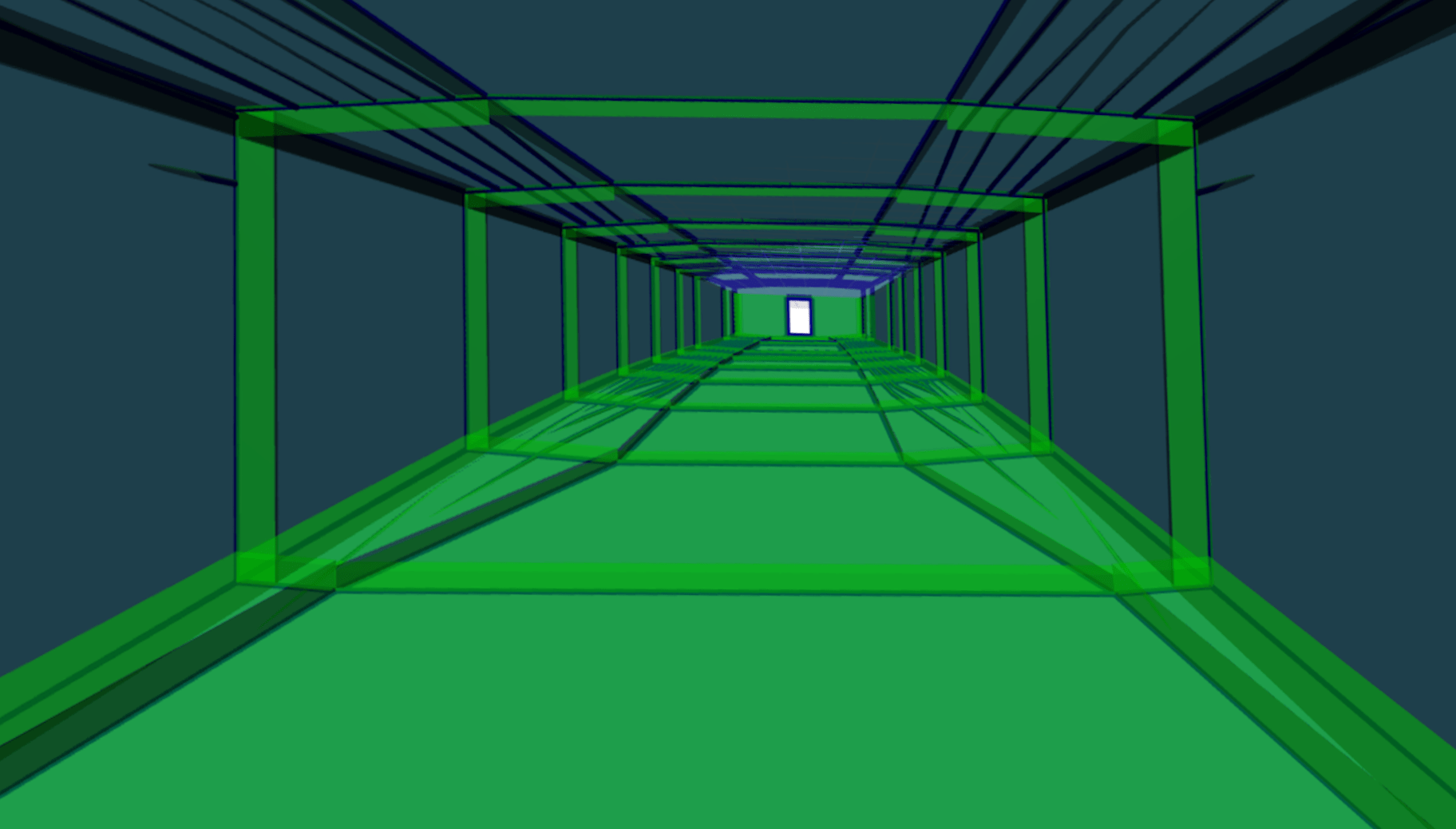
This is an extremely innovative technology. Based on the collected data, the digital model will perform all the necessary calculations to determine the current state of the represented object.
Digital twins find application in a wide variety of fields and the benefits are countless!
Why is that important?
Let’s give a closer look at our application case. We immediately get that bridges are structures with obvious strategic importance: they are meant to last through the years, and even a small inconvenience can lead to substantial troubles…not to mention the social and economic damage that would be caused by a failure of the structure.
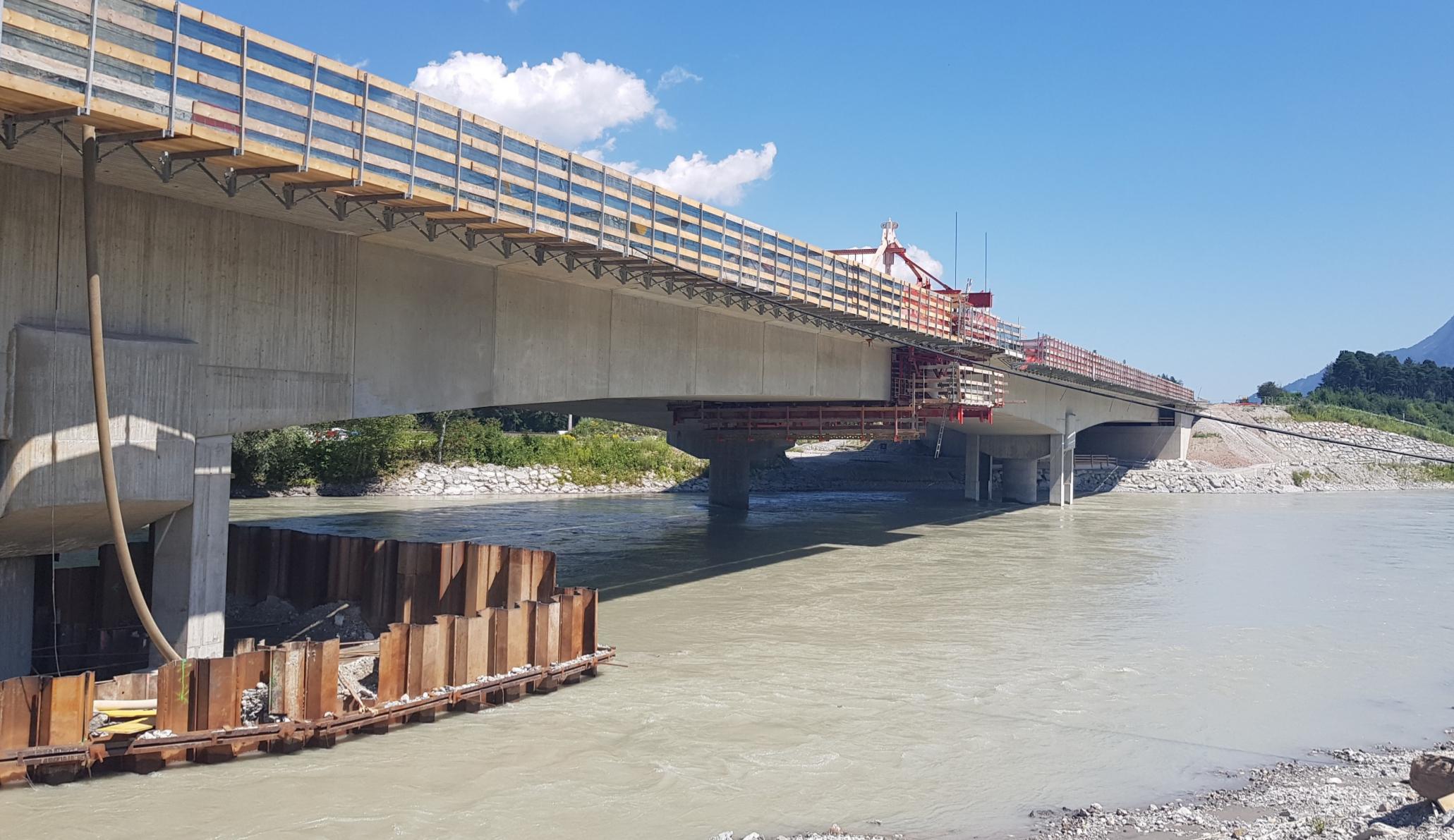
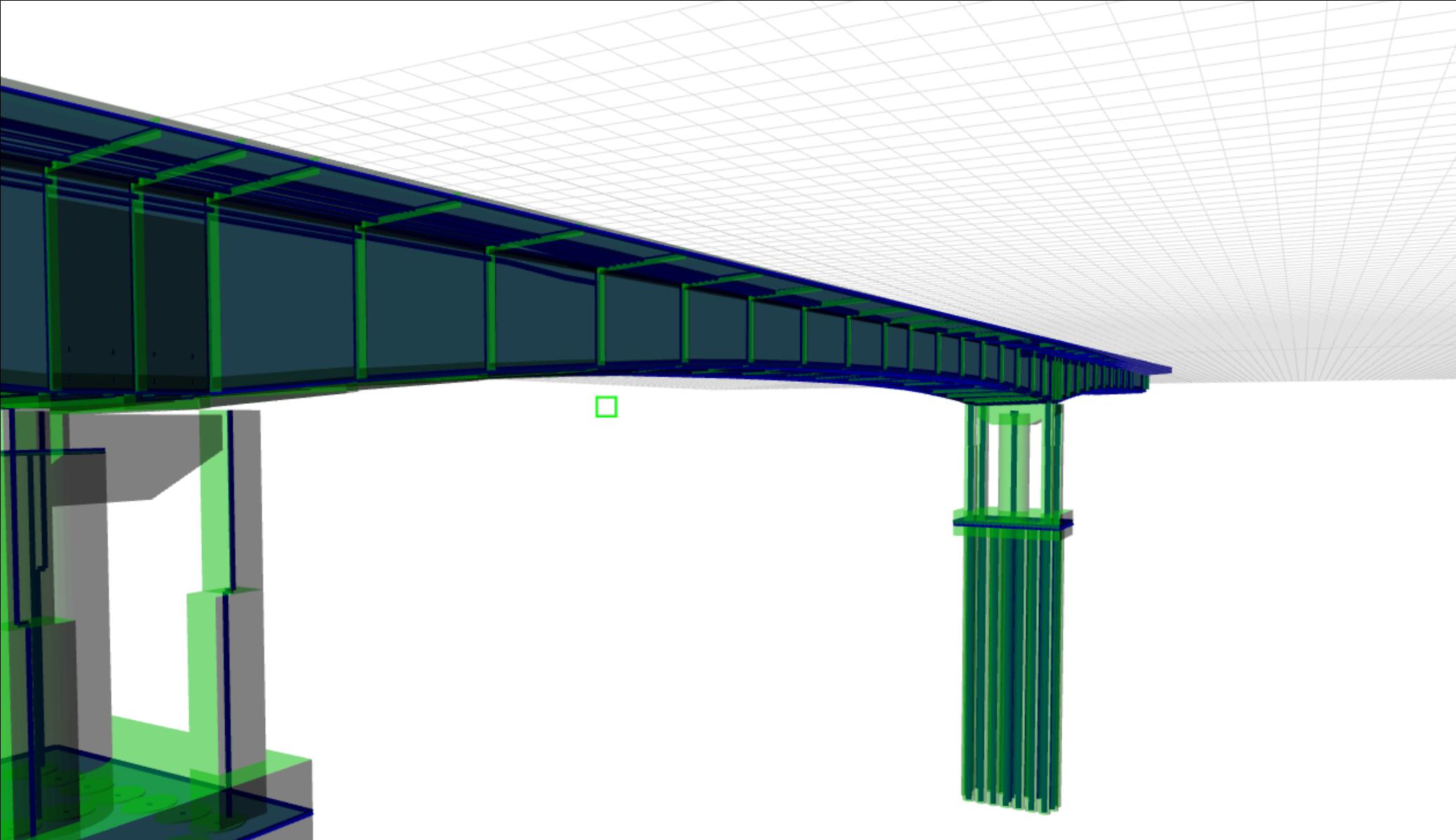
During its life, a bridge will be exposed to lots of different actions such as traffic, wind, earthquake… and it will inevitably age.
That’s why a bridge (and so does every structure) needs maintenance during its life cycle: this needs to be properly planned and executed.
Keeping the structure continuously monitored is a great help in this process: with a continuous exchange of data between the monitoring system and the model, this can be updated and offer the results on the actual stress state. And there’s more: it will be possible to compare these results with the expected ones.
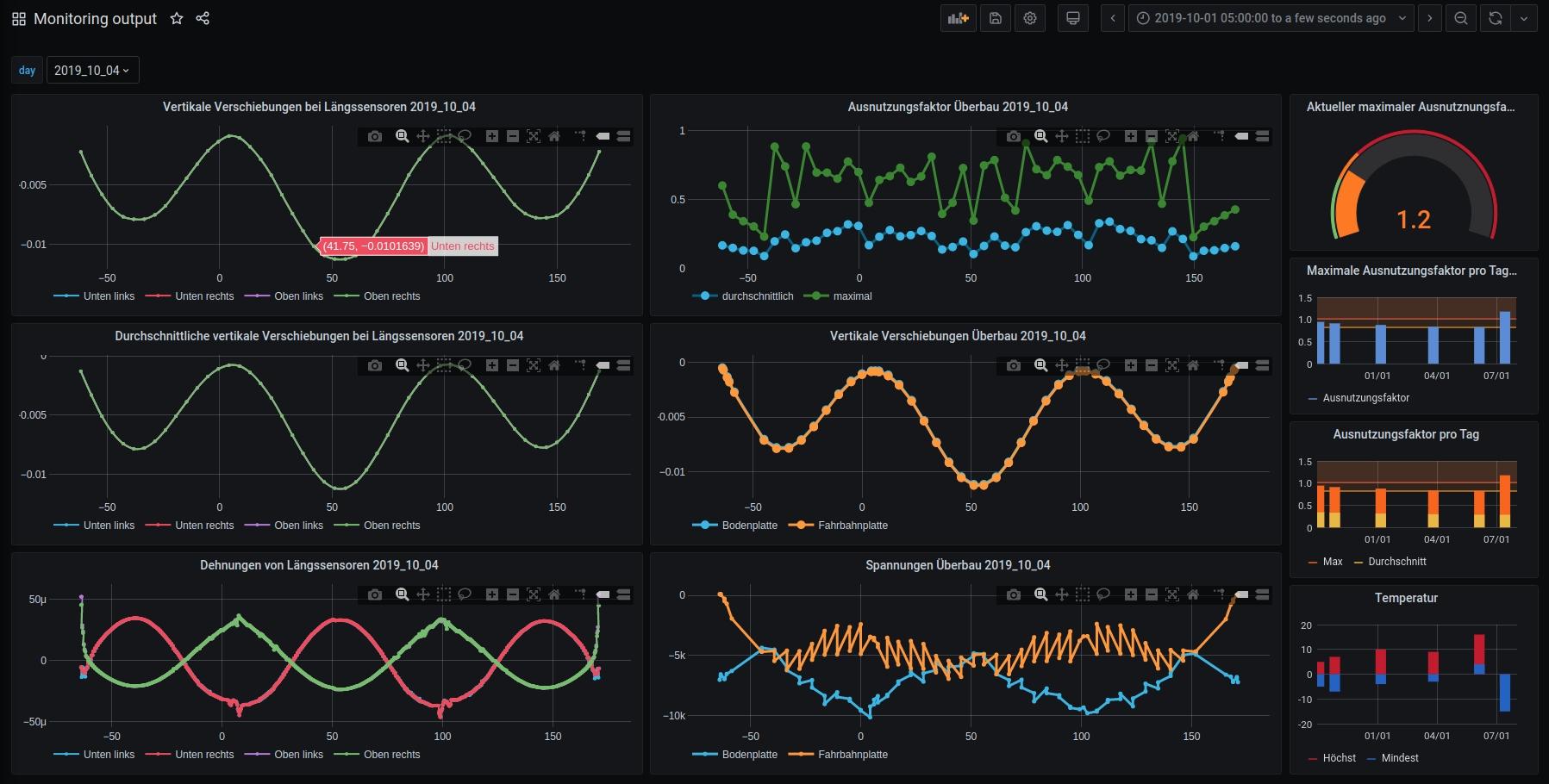
The entire load history is taken into account for the simulation of the bridge state. A very advanced finite element analysis with more than 30 steps (at least one for each construction step) is performed. The calculation takes into account anelastic strains due to shrinkage, creep and temperature. The virtual 3D model also allows to detect the local deformations and stresses induced by the pretensioned cables.
Thanks to the analysis results, it will be possible to properly plan the inspection activities on the structure.
This can also lead to an early identification of an eventual problem, giving the right time to prevent further damages!
How do we do that?
WeStatiX, being a cloud-based software, is ideal for this purpose! The model will be always available on-line, from any device, and everywhere. Through the cloud, it can access constantly to the data measured by the monitoring sensors.
CAEmate uses the most modern technologies to calibrate the digital twin on the data measured on the bridge, such as inverse analysis. We also plan to exploit technologies as Big Data Analysis and artificial intelligence algorithms to better predict the structure behavior.
We hope this project will be just a milestone in the monitoring of infrastructures!