Structural analysis is a very complex task. During its set-up, it is easy to make a mistake.
You find here a check list of the most common mistakes, and some advices on the best way to solve them.
Mistake 1: Not estimating the results of the calculation
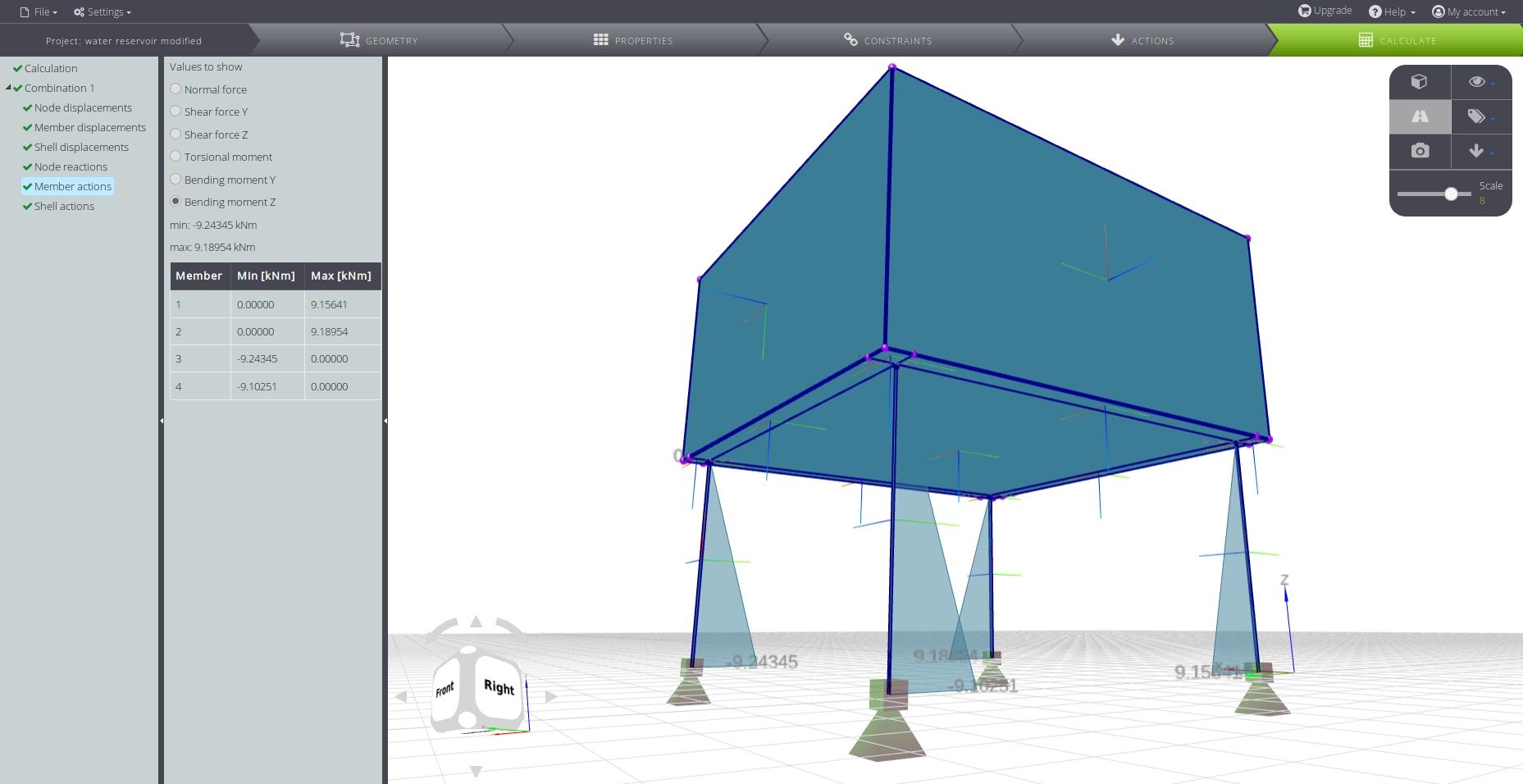
Before the start of a structural design, one of the best strategies is to estimate the outcomes of the calculation with simplified methods or at least to make an assumption on the expected results:
- How is the final structure supposed to behave and to deflect?
- What is the expected approximate trend/magnitude of the internal forces in the model?
- Are there any limits on the size of the structural parts that we need to take into account?
Very often, these infos are part of the portfolio of an experienced structural engineer. It is a good practice in every structural design office to review executed projects, before approaching the design of a similar structure. Here the library of Public Projects available in WeStatiX becomes very useful, by making available a wide range of structural models and their results.
In this way, you can analyze similar projects, get insight about the results and get confirmation on the right modeling for the type of structure you are approaching.
Mistake 2: Not using FEM and computer programs
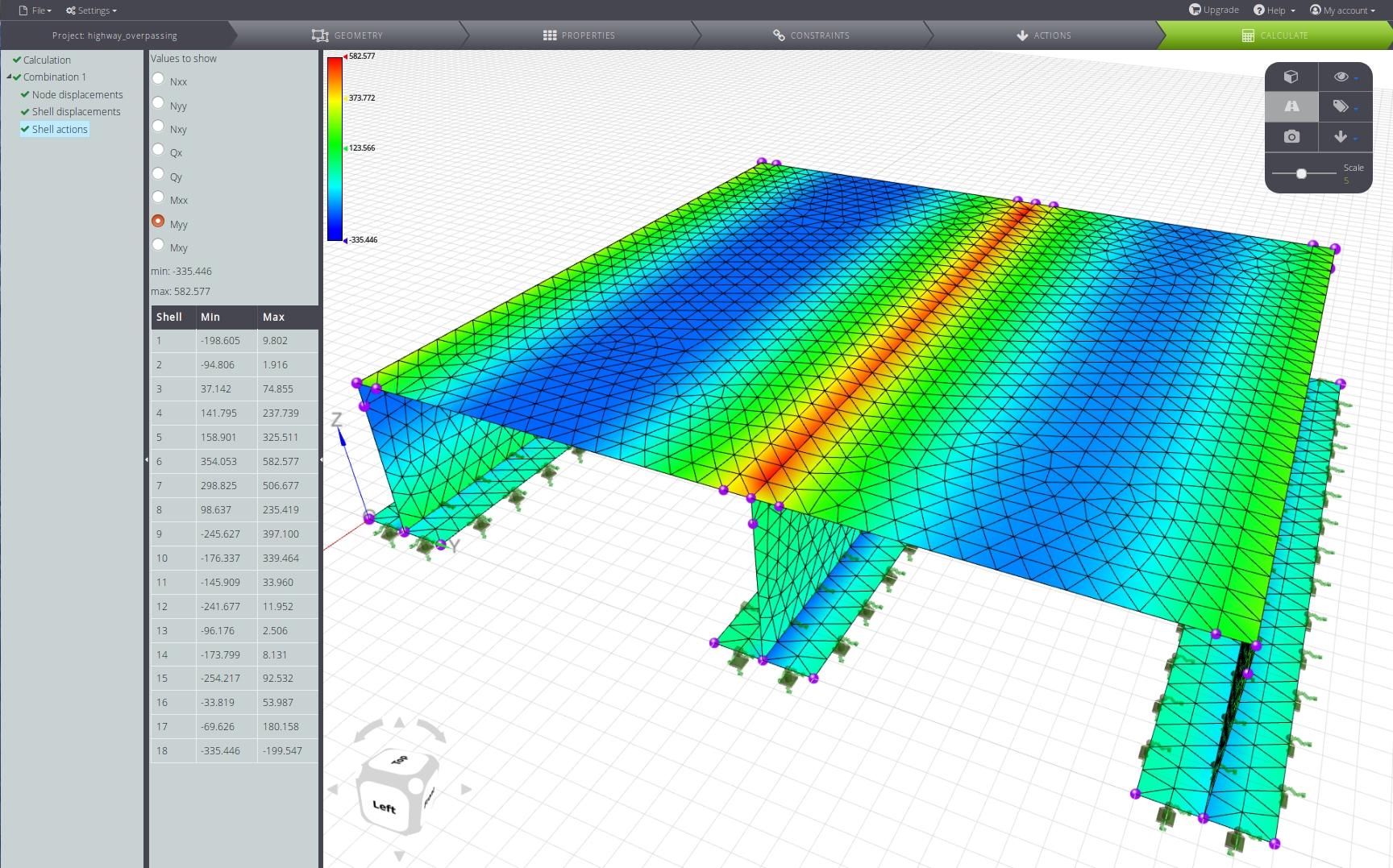
Maybe the biggest mistake in structural design is to avoid the use of CAE technology. Cloud-based structural design platforms like WeStatiX make numerical simulation affordable and available to everyone in a very efficient way. The biggest advantages of computational design methods with respect to classical procedures by hand are:
- More precise and close-to-reality structural models;
- Easy modification and optimization of the structure “a posteriori”;
- Quick and error free calculations;
- Clear and reliable storage of results.
Sometimes, experienced engineers criticize the use of advanced simulation programs. In their opinion, excessive trust in simulation tools could lead engineers to underestimate the importance of solving the problem manually. On the contrary, the use of the most advanced design technologies does not aim to replace the problem-solving ability of the engineers. The goal is to remove slow, tedious and repetitive operations from the design workflow. Tools like WeStatiX allow to carry out design procedures which are too time-consuming when performed manually. An example is the iterative optimization of the structure geometry, which can bring to significant material saving and to the increase of the structural safety.
Mistake 3: Over-constraining the structure
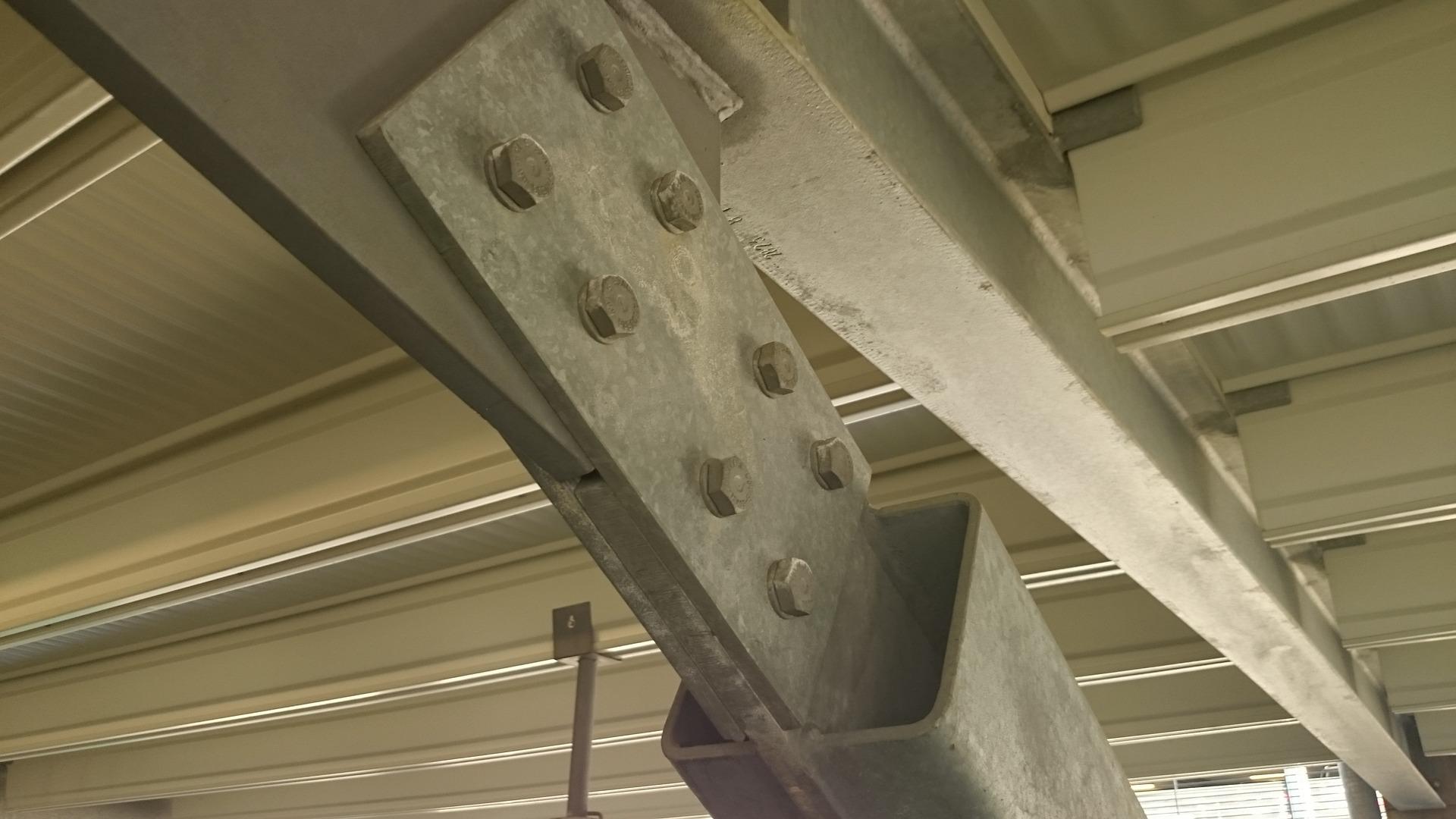
Often, civil engineers might be tempted to model joints and supports in a way not in accordance with the real behavior of the structure. Especially in the case of joints between structural steel members, perfectly rigid connections are often complex and expensive to build. Therefore, they are scarcely used for common constructions.
By modeling the structure as more rigidly connected than it is in the reality, we are actually working on the unsafe-side. More statically indeterminate (also called hyperstatic) systems tend to redistribute internal actions. Therefore, they show globally lower peaks of the bending moment. For this reason, it is good practice to carefully model the connections between structural members, walls and slabs. For example, we can use springs or hinges in order to take into account the possibility of relative rotation.
Mistake 4: Building a labile model
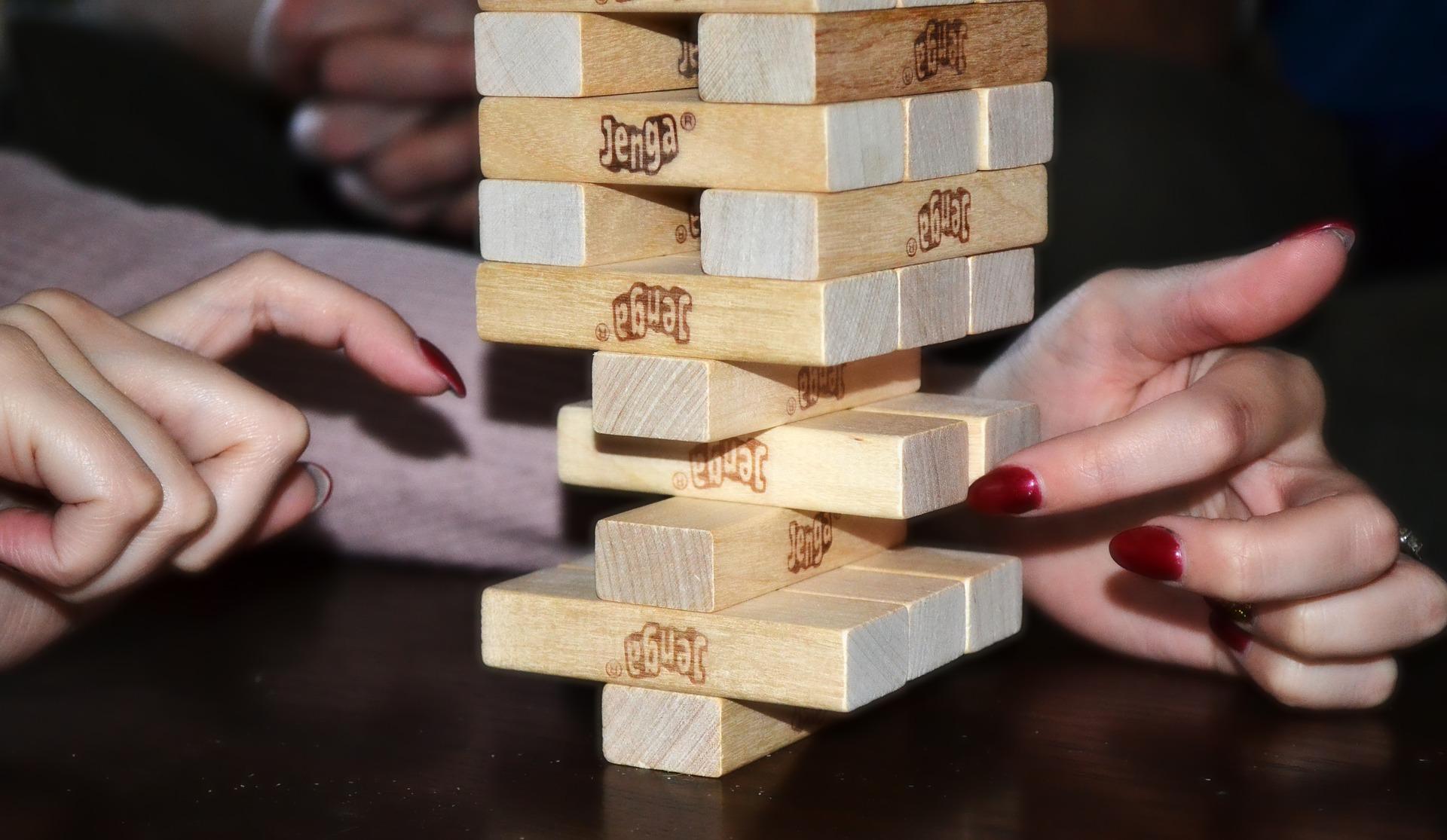
It may look as a rare error, but sometimes the structure turns out to be unstable due to supports or joints defined incorrectly.
In fact, solving the structure by FEM is not possible if the model is free to move in a certain direction. The same happens if the structure can rotate about a certain axis without giving any resistance. We should remember some simple rules, at least while dealing with simple structures:
- No beam should ever be completely free to rotate about its x-local axis. Even if no torsional load is applied to it;
- In case of structures lying and loaded in a plane (2d model), one should make sure to block the structure displacements and rotations out of the plane;
- In case of 2d models composed only by members (such as frames), the amount of static indetermination of the structure n should never be negative. We can calculate the amount with the formula n = a + z – 3s. Here, a is the number of external boundary conditions (max 3 for a fixed support), z is the number of internal constraints (max 3 for a rigid connection), and s is the total number of members in the structure.
A practical way to avoid labile models can be that of defining the released DOFs by connections or supports as springs with negligible stiffness. The influence on the results of these springs is usually negligible as well. However, the use of springs will avoid uncontrolled displacements or rotations of the structure.
Mistake 5: Generate stress concentrations and singularities
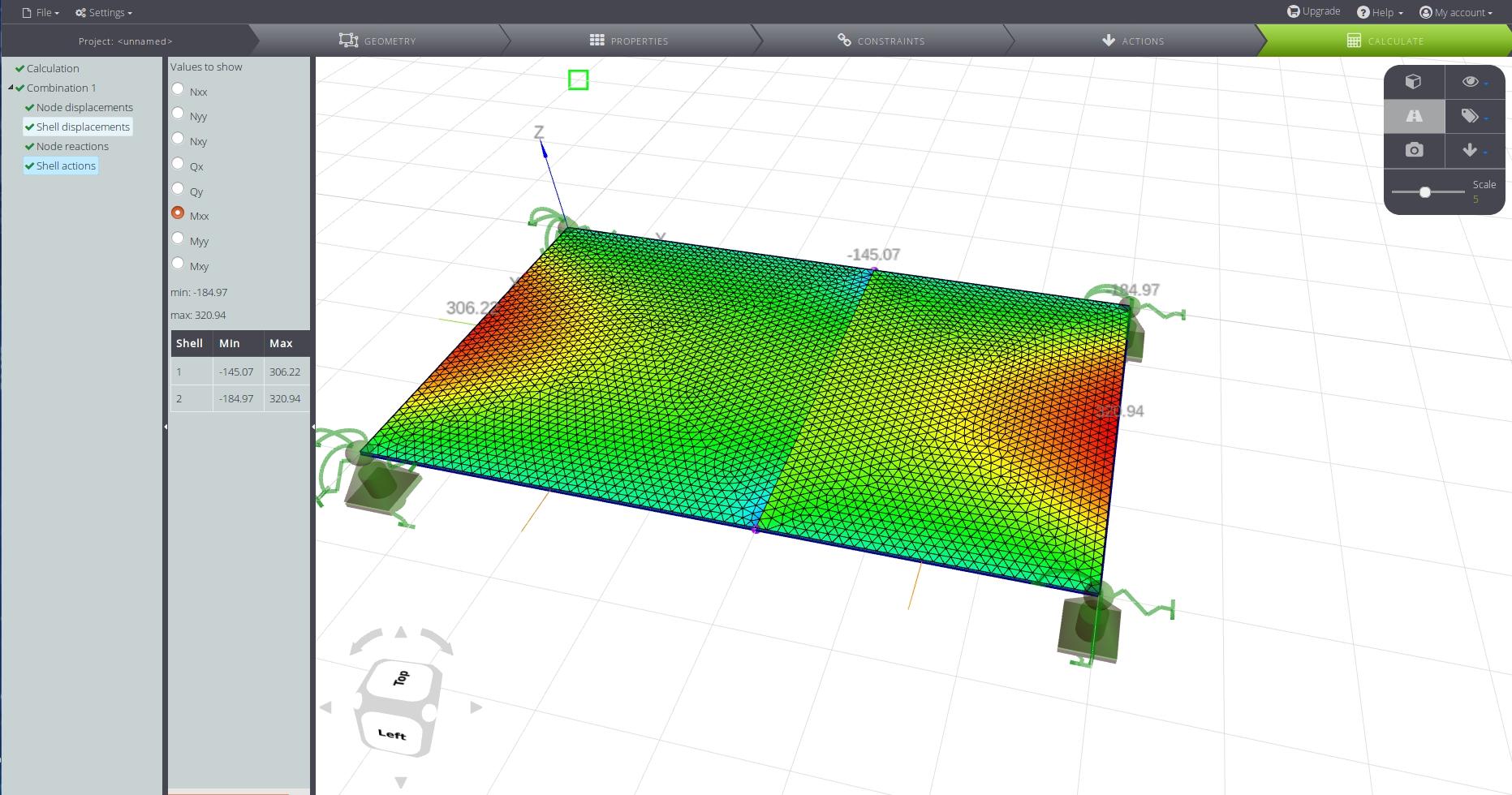
Sometimes simulations can lead to results blowing up (jumping) to very high values in small areas of the structural model. This slows down the design workflow and requires assumptions during post-processing, which might not be on the safe side. An example might be neglecting the results at these points.
In some cases, boundary conditions or constraints applied to single nodes of a shell may generate singular results. In fact, we should remember that supports are never completely rigid. Also, they are never applied to a single point of a real structure, but instead on a finite surface. Some common strategies to smooth or avoid singularities are the following:
- Replace rigid supports on shells with springs with very stiff elastic constant;
- When modeling a nodal connection (e.g. between slabs and pillars), take into account the real area of the connection;
- Perform some tests about the influence of mesh refinement on the results.